Home· · ·Techcomp college· · ·Maintenance Center
Maintenance Center
FAQ in GMP regarding Vaccine Production
FAQ in GMP regarding Vaccine Production
What is GMP?
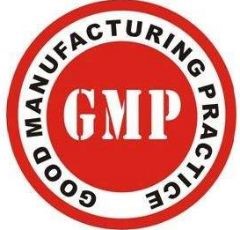
GMP, the
abbreviation of Good Manufacturing Practices, are the practices required in
order to conform to the guidelines that control the
authorization and licensing of the manufacturers of pharmaceuticals and food
and etc. GMP request these manufacturers
to implement policy, process control, quality assurance and testing to assure
the products are consistently high quality and meeting regulation.
Who established the GMP?

What is the correct concept to implement GMP?
Making poor quality products does not save money. In the long run, it is more expensive finding mistakes after they have been made than preventing them in the first place. GMP is designed to ensure that mistakes do not occur. Implementation of GMP is an investment in good quality medicines. This will improve the health of the individual patient and the community, as well as benefiting the pharmaceutical industry and health professionals. Making and distributing poor quality medicines leads to loss of credibility for everyone: both public and private health care and the manufacturer.
What is the current version of the GMP?
The current document is a revision of WHO Good manufacturing practices for pharmaceutical products: main principles, previously published in WHO Technical Report Series, No. 961, 2011, Annex 3.
What are the main requirements of the current version of GMP?
The current version GMP emphasize on:
1. Data authenticity, integrity, batch record traceability, backup and audit trail functions
2. Print function: printable records per batch
3. Data storage: To have data upload storage function and the exported data cannot be changed.
4. Authorization: With permission settings, especially where parameters can be set and only QA personnel can make any changes.
5. Prevent contamination nor cross-contamination
6. Avoid human mistakes nor errors
7. Raw materials, processes, plant facilities, process equipment, etc. have document support and fixed procedures, such as IQ/OQ/PQ for process equipment.
Which part of the process equipment is used in vaccine production?
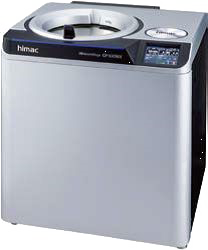
High speed and
ultra-speed centrifuges have been widely used for separating and purifying
samples in the production process of vaccine production, such as influenza vaccine,
rabies vaccine, polio vaccine, meningitis, Hib pneumonia, whooping cough,
epidemic encephalitis, hepatitis B and other vaccines. The himac
series of centrifuges from Koki Holdings (formerly Hitachi Koki Hitachi
Machinery Co., Ltd.) have been manufacturing for more than 60 years since 1955.
Its ultra-speed and high-speed centrifuges have been used by many world famous
vaccine companies for sample collection, treatment, removal of impurities,
concentration of the virus sample, and final purification.
How does the himac centrifuge help users to meet GMP requirements in data management?
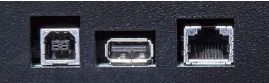
The himac centrifuges come with password access function with three access levels. Its Log Manager software provides real-time data management that can record intervals range from 10 seconds to 5 minutes. The software complies with U.S. FDA 21 CFR Part 11, with electronic signature, audit trail, data file encryption and other functions that can ensure that all data in the whole process is true, complete, traceable and in line with GMP requirements. The himac ultracentrifuge also has built-in USB and LAN port for data communication. In addition, the network version of Log Manager Software allows managing up to 16 himac ultra and high speed centrifuges and performing real-time data management and realizing remote data management.
What protection does the himac centrifuge offer in terms of sterilization and contamination prevention?
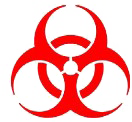
The current version of GMP put emphasis on contamination prevention. Biosafety is the primary consideration for all vaccine production. The himac centrifuge can be equipped with HEPA. Some of the rotors can be autoclaved. There are also bio-safe rotors or bio-sealed rotors, which provide bio-safety and ensure the quality of the vaccine.
If the centrifuge is used for large-scale production, can
SIP (Sterilization In Place) be done?

For large-scale production needs,
users can choose Himac's large-capacity continuous flow ultracentrifuge CC40NX
for a large number of sample purification.
The CC40NX meets the requirements of GMP. In addition to the conventional CIP, CC40NX has the unique SIP
(Sterilization In Place) function for disinfection and sterilization which can
enhance the efficiency of sterilization and thus the quality of vaccine is
guaranteed.